Getting things done.
We create high quality products that work for your audience and your business
Whatever you do, the way you express your brand identity and story can make all the difference. Let’s create the better way to express your brand and products, together.
What we offer
☞ Logo Emblem
☞ Overlay Panel & Push Button Information
☞ Part & Turnkey Assembly
-
Overlays are a vital printed interface layer feature in touchscreens and membrane switches, as well as a standalone durable label that provides both protection and a surface for graphic printing, resulting in a functional and user-friendly interface.
Graphic overlays are often the first thing a consumer perceives when interacting with a product, and they can leave a lasting impression. We have the industry's most comprehensive overlay selections, including selectable texturing, printing, embossing, coatings, adhesives, dead fronts, and backlighting to build a unique overlay solution.
We can design cutting-edge, ready-to-use control panels with a range of graphic overlay options to meet any specification.
-
To mould high-precision plastic parts with remarkable colour and design, in-mould decorating is used. The process relates to laying an appliqué – a pre-made form made from a printed sheet of plastic that is then moulded and cut to size – into an injection mould and moulding behind and around the appliqué. It offers the advantages of injection moulding with those of innovative printing technology.
For generations, people have utilized ornamental patterns in moulds to create things, and the technology is now being used in the injection moulding business. IMD allows a company to make plastic parts with an almost endless range of look alternatives. Unusual colours, patterns, and textures can be used to create parts. Realistic and even holographic visuals can be instilled into parts. Parts that are opaque in one region, translucent in another, and obvious in another can be made.
There are portions that glow in the dark, in the sun, or only under certain circumstances. Parts having a hard coating in one region and a soft-touch coating in another, or any combination of the above, are available. Generally, anything that can be printed can be used in the IMD process. All of this is accomplished without the use of a label or decal since the decorative feature is moulded into the moulded plastic section.
-
Membrane switches are a sort of human-machine interface that is made up of numerous layers of flexible plastic films or other materials. The surface of these plastic films is printed or laminated with conductive materials and graphic inks. They operate by closing or opening an electric circuit for a short span of time.
Membrane switches are ideal for a wide range of applications, including domestic appliances and industrial equipment interfaces, due to their compact and efficient structure.
-
PVD (Physical Vapour Deposition) coating, also known as thin-film coating, is a process in which a solid material is vaporized in a vacuum and deposited onto the surface of a part.
These coatings are not simply metal layers though. Instead, compound materials are deposited atom by atom, forming a thin, bonded, metal or metal-ceramic surface layer that greatly improves the appearance, durability, and/or function of a part or product.
-
Two-shot injection moulding is cost-efficient and improves quality and manpower reduction.
Since this two-step method only requires one machine cycle rather than multiple sessions, rotating the first mould out of the way and installing the secondary mould around the product costs less and takes fewer man-hours. This strategy is less expensive for any production line and can yield more items per run.
Two-shot injection moulding manufactures quality products
When compared to painting, which can typically be wiped off, the two-shot injection technique increases colour quality. This eradicates the need to paint while also enhancing the colour's life. As a result, higher-quality products arrive on the market, which appeals to consumers and often leads to increased sales. The two-shot moulding process also combines two materials in a single step, eliminating the need for adhesives and resulting in a stronger bond.
Furthermore, products can be ergonomically engineered, allowing for more efficient fittings and fewer misalignments. process, creating a stronger bond without the use of adhesives. Additionally, products can be ergonomically designed, which inherently allows more efficient fittings while reducing misalignments.
-
Moulded plastic parts provide a variety of design alternatives as well as long-term durability in tough environments.
Our plastic injection moulding technique is the foundation of our plastic manufacturing, and our team of experts can guide you with the procedure. We also provide compression moulding, which is a popular choice for buttons, keypads, gaskets, and a variety of other user interface and assembly components.
Last but not least, all the engineering plastic (PC, PMMA, ABS, PBT) and double injection are available here as well.
-
Soft Emblem is a universal patented and licensed technology in the badging market that allows for the creation of three-dimensional and flexible emblems, badges, and labels with unrivalled beauty and elegance using basic and sophisticated contour shapes.
The soft emblem system has a major footprint in the Automotive and Household markets due to its unique materials and patented production technique. Versatility and creativity.
• Superior to any other existing technology in terms of attractive chromed effect
• No restriction on finishes, textures, or colour combinations
• Ability to create emblems for pressure-sensitive adhesive or thermal adhesive applications
• Attribute with particular traits and/or finishes using the same toolings
• Impresario with various toughness using the same toolings
• Wide array of possible raw materials for the perfect fit to the end-user requirements
• Prototype that is both rapid and inexpensive
-
-
-
-
-
-
Our exceptional design support, colour-matching, and production skills can assist you in creating a bespoke product nameplate that your company will be proud of.
Every tailor-made nameplate is created to match your particular requirements and is designed to endure the elements. We're here to help you get the job done as quickly and creatively as possible, no matter where you are in the process. The options are limitless.
To spark some ideas for your personalised nameplate, look through our gallery to see examples of the various designs and features we provide both for metal nameplates and plastic nameplates.
-
-
-
-
-
-
-
“It was a highly organised and professional working with TTP.”
— Chitpanu K.
Director & Business Partner, RiddleGate
-
Front Panels or Graphic Overlay or Inlay or Display
-
In mold decoration/ Film insert molding / PSI
-
Panel Membrane Switch
-
Sputtering Plate or Vacumn Metalizing Products (Sputtering PVD)
-
Plastic Double Injection
-
Plastic Injection Moulding
-
Soft Emblem
-
Plastic Emblem
-
Metal Emblem
-
Heat & Cool or Rapid Heat Cooling (RHC)
-
Metal Stamping
-
Metal Label & Nameplate
-
Light Guide or Back Lighting
-
Doming Resin
-
Low Pressure Moulding
-
Lathe Products
-
Sticker & Label
-
Rubber Keypad
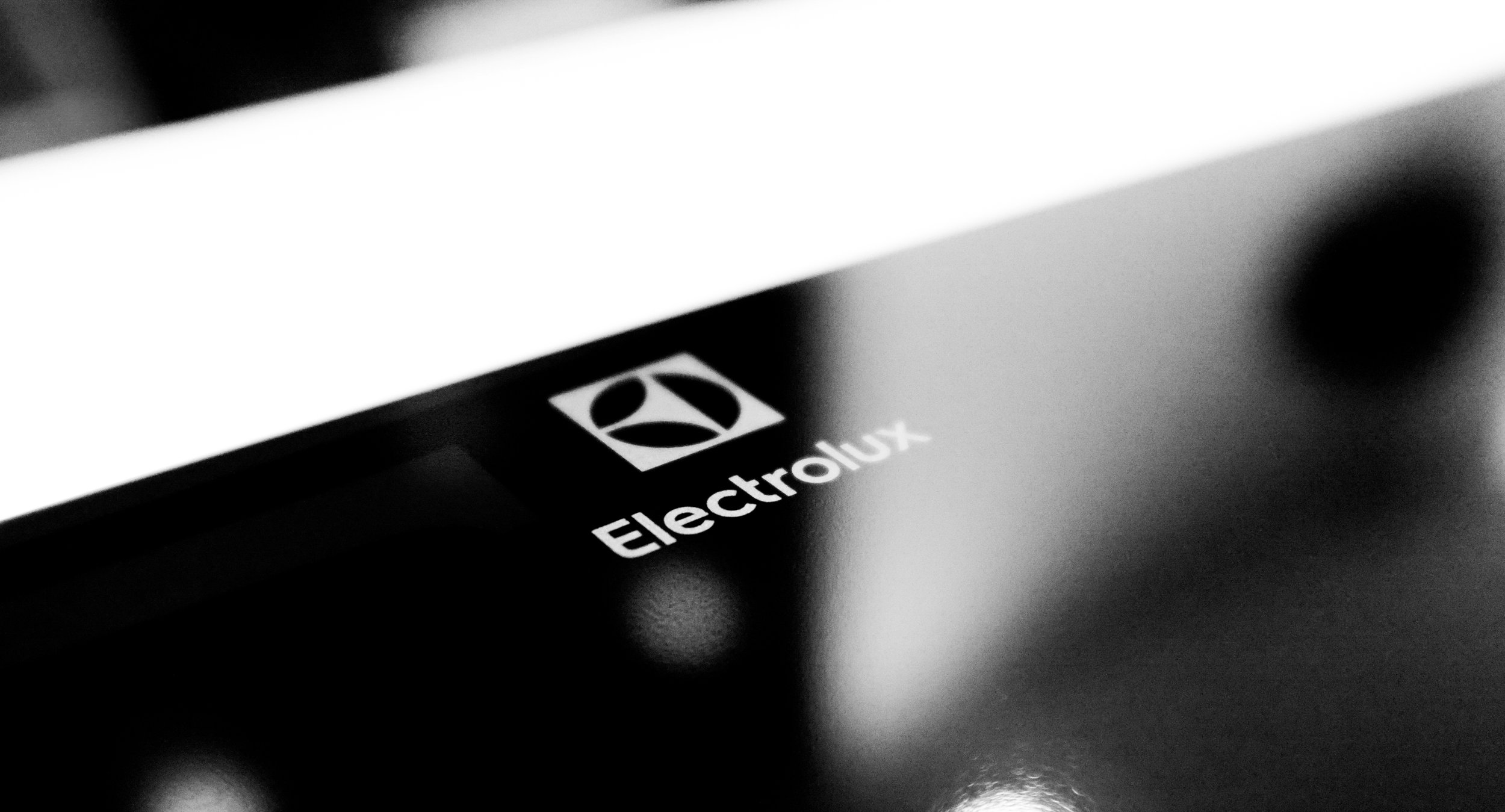
Let’s work together.